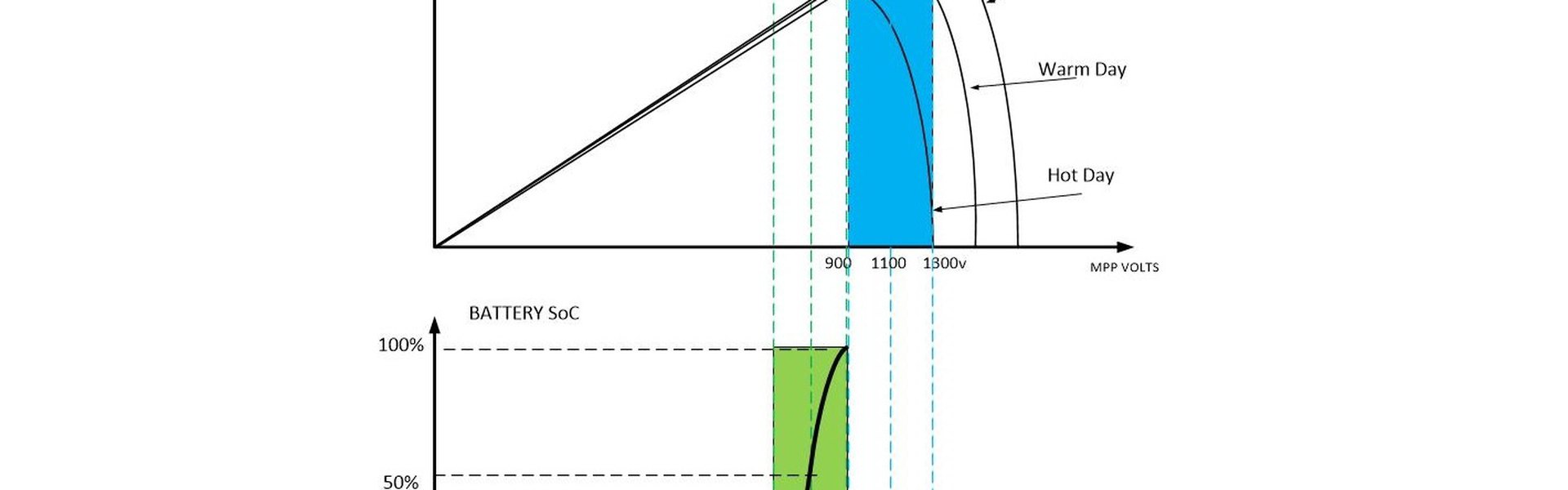
Voltage Mapping: The Key to Making DC-Coupled Solar + Storage Work
How Galvanic Isolation Helps Bring Solar and Storage together on the DC-side of the inverter
The coupling of Solar and Storage on the DC-side of the inverter makes so much intuitive sense. After all, solar panels and batteries are both DC devices. But yet, today, most Solar and Storage projects are still AC coupled, where PV energy is first converted to AC while another inverter in front of the battery converts that AC power back to DC to charge the battery, leading to higher losses and equipment costs.
The Voltage Mapping Challenge
If pairing Solar and Storage via AC coupling is so inherently inefficient, why is it so common? One answer is this: The dissimilar voltage ranges where Solar PV and batteries typically operate and the conditions that govern these voltage ranges can be more easily handled via AC Coupling. That is, until now. This match in voltages and operating conditions is shown in the graphic below.
The DC bus voltage is adjusted to harvest maximum power from the PV array and depends on type of PV panels, temperature and insolation. The voltage on the battery rack is defined by the state of charge (SoC) and can vary widely from one battery manufacturer to another, particularly for different battery chemistries, i.e. lithium ion, vanadium flow etc.
The DC bus voltage coming from the PV array at the MPPT can be fundamentally different from the voltage required to control the SoC of the battery. For example, a typical 1500-volt PV array will generate voltage anywhere between 900 to 1300 volts while a typical, utility scale lithium ion battery may have an SoC range somewhere between 600 to 900 volts. To make this “mismatch” in voltage more challenging, these ranges move completely independently of one another.
How do DC-Coupled Solar + Storage Systems Work?
DC-coupled battery energy storage systems (BESS for short) work as follows: The solar PV array generates electrical energy. The solar panels are wired onto a DC-bus connected to both the battery racks and a grid-connected inverter. When the supply is equal to demand all PV energy is exported to the grid. When supply exceeds demand, the extra energy is stored in the batteries and when demand is higher than the available PV supply, the deficit of energy is taken from the battery.
A system controller dictates the behavior of the BESS, i.e. whether the battery charges or discharges (Click here to learn more about the role of the system controller in BESS.). However, in order to charge or discharge battery, the issue of the voltage mapping must be resolved. This issue is addressed by design in AC coupled systems because the PV and battery each have their own inverter and AC switchgear to allow this “mapping” to occur on the AC side of system. Problem is, this solution comes at a cost of more expensive Solar + Storage systems, with lower efficiency and the inability to capture clipped energy. (Click here to learn more about the advantages of DC-coupled Solar + Storage systems versus AC coupled topologies.)
The Voltage Mapping Solution: Galvanic Isolation
The voltage difference between the battery voltage and DC bus voltage may be as large as 700 volts for lithium ion batteries and as much as much as 1250 volts for vanadium flow batteries.
Here at Alencon, we’ve addressed this challenge by building a galvanically isolated DC-DC optimizer that allows these two very different, independently moving voltage ranges to be mapped into one other automatically. Alencon DC-DC optimizers perform two types of voltage mapping: static and dynamic.
Static voltage mapping equalizes the fundamental difference in the mean of the two voltage ranges: the PV MPPT range and the Battery SoC range.
Dynamic voltage mapping is used to equalize the PV and Battery voltage within their variable ranges during operation of the system under various weather and energy demand conditions.
The static range is achieved by providing a galvanically isolated DC-DC optimizer, such the as the SPOT or BOSS, The Alencon DC-DC optimizers achieve galvanic isolation by placing a high frequency isolation transformer on each input. As part of our mass customization manufacturing process, we can easily configure the windings on these transformers to map virtually any PV voltage range into almost any battery SoC range, thus rendering the SPOT or BOSS essentially battery chemistry agnostic. These transformers completely separate the input from the output, managing the fundamental voltage difference between the PV and the battery. In the example given above, the mean of the two voltage ranges that differs by 350 volts are being mapped.
The dynamic mapping of +/- 200 volts to match PV voltage during weather variations with the varying SoC of the battery is carried out by the Alencon DC-DC optimizers internal electronic and firmware controls. Having mapped the fundamental difference between input and output voltage, the input and output ranges can then be covered independently having separated them electro-magnetically.
Another way of looking at this solution is that the SPOT or BOSS essentially act as DC-transformers of sorts, bringing in one range of DC voltage, converting it to AC internally, manipulating it and then outputting it as another range of voltage all together. It is basically as if we have taken one of the large transformers out of an AC coupled Solar + Storage system and placed them infront of the grid tied inverter. Thanks to our patented design we are able to achieve this in a highly efficient, compact and cost-effective manner.
So Why Should You Care?
Some of our non-technical readers may have found some of reading above to be a bit challenging to absorb. To translate the technical explanation above into real world impact, the ability to DC-coupled Solar + Storage in a cost effective and technically feasible is a major factor in expanding our reliance on clean, renewable power. In particular, today, most new PV projects are based on 1500-volt PV arrays, but the voltage on batteries is below that, so the need to bridge the voltage gap between PV and storage is absolutely essential to making renewables more reliable, dispatchable energy resources. Additonally, this approach to DC-coupling allows grounded PV systems to be easily coupled with floating batteries on the DC-side of the inverter.